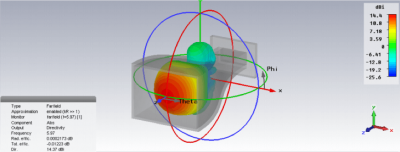
Design & Test a 3D Printed Horn Antenna
April 19, 2018What is a 3D Printed Horn Antenna?
The horn antenna is an antenna that consists of a flaring metal waveguide shaped like a horn to direct radio waves into a beam. 3D printing is a fast-growing technology for rapid prototyping of mechanical structures at a relatively low cost. This enables quick production and demonstrations of experimental models and measurement results for innovative ideas. In this application note, we describe our experiences fabricating a pyramidal horn antenna using 3D printing technology.
Building the 3D model
3D printing is a novel prototyping technology, but the model of the horn antenna will be a traditional horn antenna. There are several ways to determine the best dimensions for the horn antenna. The first approach is to calculate the dimensions according to a target frequency using equations.
The second approach is to create your model based on an existing design. For example, you can find many antenna reference designs online with different characteristics, and then tune them for your own application or requirements.
When creating the models, we can utilize the unique capabilities and advantages of 3D printing. For example, in our demonstration we’ve added curvature to our model with the objective of reducing ripples in the frequency response.
Simulation Results
The following simulation results show the S11, the radiation pattern, and a 3D plot of directivity in turn.
The first pair of plots shows a comparison between S11 of a straight, conventional structure (top) and a curved structure (bottom).
The smoother transition reduces ripple in the transmitting region by lessening the reflection. Subsequent plots are for the curved horn antenna model.
As can be seen in the plots below, the directivity estimated by the simulation is 14.37 dBi.
Fabricated Model
The 3D antenna model was printed. The turnaround time was approximately 2 weeks and the cost was approximately $200. The left picture is before painting; the right picture is after the interior of the horn was painted with a conductive paint.
Simulation Results
After connecting the model to a coax-to-waveguide adaptor, we used the CMT Planar 804/1 to measure the return loss (S11) of the 3D printed horn antenna assembly. Calibration was performed at the cable end of the coax-to-waveguide adapter.
The waveguide adapter we used is WR-137, which works from 5.85 GHz to 8.2 GHz. The simulation result predicted that the reflection coefficient would be lower than -20 dB, and our 3D printed horn antenna demonstrated a reflection coefficient of less than -16dB for frequencies higher than 5.85 GHz. It’s a satisfying result considering the many differences between simulation and the real world.
Tips for 3D Printed Horn Antennas
There are several key factors related to the performance of 3D printed horn antenna.
The first is the accuracy of the 3D printer. This will mainly affect cut-off frequency and directivity since the dimensions determine the modes of wave that can propagate in the horn antenna. The second is the smoothness of the printing material and technology being utilized. As discussed in Bryan Willis’s dissertation [1], smoothness has a considerable impact on the transmission of the antenna. The roughness of the surface will introduce more reflections and worsen the match. In addition, the rough surface will make painting harder since the paint may not be applied evenly.
We used a prime, gray material instead of regular plastic to maximize the smoothness of the surface. Printing technologies such as stereolithography (SLA) will result in an even smoother finish. Furthermore, applying three layers of copper paint instead of one will improve the performance of the horn antenna since there will be less reflection. C.R. Garcia’s paper [2] provided measurements result for comparison between a one-layer-painted antenna and three-layer-painted antenna; the paper shows that increasing painting layers will lead to a smoother surface which results in better transmission.
Bibliography
- J. Willis, “COMPACT FORM FITTING SMALL ANTENNAS USING THREE-DIMENSIONAL RAPID PROTOTYPING,” The University of Utah, May 2012.
- R. H. T. a. J. B. C.R. Garcia, “Effects of extreme surface roughness on 3D printed horn antenna,” 6th June 2013.
Comments (0)